The Story of Lean Production-- Toyota's Secret Weapon in the Global Car Wars That Is Now Revolutionizing World Industry
ByJames P. Womack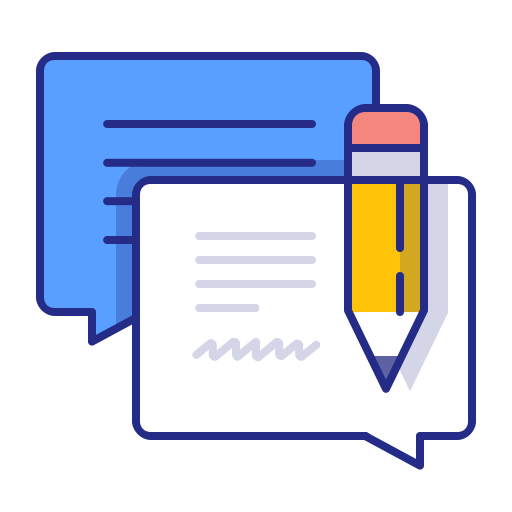
★ ★ ★ ★ ★ | |
★ ★ ★ ★ ☆ | |
★ ★ ★ ☆ ☆ | |
★ ★ ☆ ☆ ☆ | |
★ ☆ ☆ ☆ ☆ |


Check out Audiobooks.com
Readers` Reviews
★ ★ ★ ★ ★
paul cutler
This is the best unbiased insight into the operations of the auto industry with great insights into the best practices for design, manufacturing, and marketing. The lessons taught are applicable to any manufacturing industry, especially one that operates on a global basis. It shatters myth, mysteries, and legends and replaces it with scientific data that solidifies the concepts of lean business. A must read for all manufacturing professionals at any level.
★ ★ ★ ★ ☆
jocylen
Book is a good discussion on Lean Manufacturing in the automotive industry. Only issue is it is getting dated (circa 1990) and needs to be updated. A lot of what the books future expectations are history.
★ ★ ★ ★ ★
madison
This book provides an excellent introduction to lean techniques. I am college student majoring in mechanical engineering and needed something that could give me an overview of lean production and help me understand how it differs from mass production. The book certainly meets that criteria. While it does not give many case studies of how companies can convert to lean production, "Lean Thinking" by the same authors does do that and is also an excellent book.
The authors performed many years of research before publishing their data and can provide hard numbers to back up their claims that lean production is simply a better method. If you're looking for something to introduce you to lean production, this is the book to get.
The authors performed many years of research before publishing their data and can provide hard numbers to back up their claims that lean production is simply a better method. If you're looking for something to introduce you to lean production, this is the book to get.
The No-BS Blueprint to Building a Life-Changing Business :: Turn Your Ideas into Reality and Become a Wildly Successful Entrepreneur :: Eine Scheibenwelt-Erzählung (German Edition) :: Feet of Clay: A Novel of Discworld :: Inspiration and Advice from over 100 Makers - and Entrepreneurs
★ ★ ★ ☆ ☆
eduardo tenenbaum
This book is certainly a kind of milestone in the auto literature history. Yet, for today's readers it is probably not the first choice to read. The huge impact the book had and its benefit is that it rightly lifts the Toyota production system (TSP) to the status of the Ford assembly line and other revolutionary inventions in production organisation. It declares TSP as the successor of Fordian mass production.
There were books about the TPS before, notably the book of Taiichi Ohno in the mid-1980s, one of the principal creators of TSP, but the audience was not sure about its real significance. TSP came a long way from the 1950s and its development was evolutionary rather than instantaneous. Its deployment was painstaking and required a lot of Japanese perseverance. The Japanese deserve all the credit for pulling that through. With this book the MIT plays a kind of authority in the history of production technology and bestows TSP official recognition. For today, the book is still interesting to read from a historical perspective but if you want to get into the details of the history of TSP Fujiomoto's "Evolution of a Manufacturing System' is probably the best choice today.
The problem with "the machine that changed the world" (besides its title) is that is to one-side and totally uncritical of the Japanese manufacturers. This was probably necessary to ring the alarm bells at the time but it was not justified. The decade following the publicaton of the book would show that the Toyota system involved certain risks and idiosyncracies of the Japanese market context. (It is interesting to note that only Cusamano, who worked on the product development part of the MIT project without being an author of the book, acknowledges the high risk of escalating design costs that would later push Nissan to the verge of bankruptcy). For Madzda and Mitsubishi TPS was very problematic as well. While the authors are totally concentrating on production systems, which is ok, it is not the single success factor in auto industry as the authors implicitly suggest. They almost treat cars as a commodity, exchangeable, only attributed by quality and certain design criteria. The ranking the book presents is based on production efficiency (first, Japanese, second come US firms, and the Europeans are the worst of the worst). Yet, it makes it very difficult to understand the sustained success of the French and German car industry. Admittingly, the UK industry went downhill, but at the same time Spain became one of the biggest auto production location in the world. What the authors (professors of production technology) neglect is that the European market and the Japanese market are very different from the US market.
First, local markets have very different preferences. Auto companies in Europe, Japan and the US have a strong home market advantages by perceiving and responding to these home preferences much earlier. Second, local requirements are very different as Porter notices in his book about the competitive advantage of nations. For instance, German autobahns require top performance, high fuel prices in Europe make European cars more fuel efficent and so on. The real success of the Japanese in the US came when they started to develop cars solely for the US market needs which were then manufactured with the quality the TSP system achieves.
As a result of the Japanese focus on the US market, they were never really successful in Europe, where performance, innovative technology and design ranks somehow relatively higher than in Japan and the US.
Yet, Toyota's sustained global success indicates that they have created a marvellous production system that is worth studying. But it is not very easy to understand in all its parts, that is has not been until today fully adopted by companies outside Japan demonstrate its complexity or dependence on the Japanese market context
There were books about the TPS before, notably the book of Taiichi Ohno in the mid-1980s, one of the principal creators of TSP, but the audience was not sure about its real significance. TSP came a long way from the 1950s and its development was evolutionary rather than instantaneous. Its deployment was painstaking and required a lot of Japanese perseverance. The Japanese deserve all the credit for pulling that through. With this book the MIT plays a kind of authority in the history of production technology and bestows TSP official recognition. For today, the book is still interesting to read from a historical perspective but if you want to get into the details of the history of TSP Fujiomoto's "Evolution of a Manufacturing System' is probably the best choice today.
The problem with "the machine that changed the world" (besides its title) is that is to one-side and totally uncritical of the Japanese manufacturers. This was probably necessary to ring the alarm bells at the time but it was not justified. The decade following the publicaton of the book would show that the Toyota system involved certain risks and idiosyncracies of the Japanese market context. (It is interesting to note that only Cusamano, who worked on the product development part of the MIT project without being an author of the book, acknowledges the high risk of escalating design costs that would later push Nissan to the verge of bankruptcy). For Madzda and Mitsubishi TPS was very problematic as well. While the authors are totally concentrating on production systems, which is ok, it is not the single success factor in auto industry as the authors implicitly suggest. They almost treat cars as a commodity, exchangeable, only attributed by quality and certain design criteria. The ranking the book presents is based on production efficiency (first, Japanese, second come US firms, and the Europeans are the worst of the worst). Yet, it makes it very difficult to understand the sustained success of the French and German car industry. Admittingly, the UK industry went downhill, but at the same time Spain became one of the biggest auto production location in the world. What the authors (professors of production technology) neglect is that the European market and the Japanese market are very different from the US market.
First, local markets have very different preferences. Auto companies in Europe, Japan and the US have a strong home market advantages by perceiving and responding to these home preferences much earlier. Second, local requirements are very different as Porter notices in his book about the competitive advantage of nations. For instance, German autobahns require top performance, high fuel prices in Europe make European cars more fuel efficent and so on. The real success of the Japanese in the US came when they started to develop cars solely for the US market needs which were then manufactured with the quality the TSP system achieves.
As a result of the Japanese focus on the US market, they were never really successful in Europe, where performance, innovative technology and design ranks somehow relatively higher than in Japan and the US.
Yet, Toyota's sustained global success indicates that they have created a marvellous production system that is worth studying. But it is not very easy to understand in all its parts, that is has not been until today fully adopted by companies outside Japan demonstrate its complexity or dependence on the Japanese market context
★ ★ ★ ★ ★
nuno tuna
This book is probably the best book on the automobile industry with respect to the rise and fall of the American and European auto manufacturers vis-a-vis the Japanese. While the Americans have made great strides in recent years the roots of their near demise are clearly exposed in this book. Some European manufacturers have learned from their mistakes but many have not and still produce cars that are more fabled than truly well designed and executed. The English auto industry took this to their grave. The Germans are still struggling to get their cars to equal their price premium in all respects not just performance or handling. In the end the Japanese have taught the whole world what it takes to deisgn and build a car.
★ ★ ★ ★ ★
sarah mason
While this book has been touted as an enlightening view of lean production and how it beat mass production in manufacturing it is also extremely instructive for anyone who is interested in the auto industry in general. It not only shows how the west's failure to listen to Demming allowed the Japanese to revolutionize the industry, it also pokes a few holes in the hallowed European "quality" myth particularly the German manufacturers. For westerners it also raises the curtain on the Japanese domestic auto business which I found very enlightening.
★ ★ ★ ★ ★
ja net
A visiting professor recommended this book when I asked him about the LEAN philosophy. What is great about this book is how it introduces the birth of not only the LEAN concept, but also the MASS PRODUCTION which preceded and still dominates the world of manufacturing. With its timeline based structure, this book shows how and why the complex automotive industry is changing to LEAN. All other industries tend to follow...
★ ★ ★ ★ ★
skiedragon
Wow!!! It is amazing how everything Womack wrote in this book about the auto industry's future actually came true. What insight!!! This is also an excellent look at lean production, and how it extends beyond the walls of the organization to all of the organization's suppliers, and also to the customers.
★ ★ ★ ★ ★
edward
This book contains all the seeds of the Lean Production Ideas. A must for the serious Lean Practitioner. This is the most influential book on the subject. However it needs a great deal of study and deep understanding but it's worth it for the insight and Lean foundations it provides.
★ ★ ★ ★ ☆
aviles2002
Lean production started with Henry Ford's car for the masses. Toyota took the old idea of customization combined with mass production to create their mass customization model. Quality is important in the product and focus on what is important to the client allows us to know what qualities make the most difference."If it aint broke don't fix it." Providing an affordable product was 20th century sales. Improving the improvements that are critically important to the client is 21st century marketing. The book proves it through the automotive manufacturing model.
★ ★ ★ ★ ★
jeremy rathke
This book kept my interest. The lean production concept used in Japan automakers was clearly demonstrated as a superior way to American mass production. I can see how lean production can be transferred to other industries than auto manufacturing. The book also contained the history behind mass production and lean production, which was interesting. The insight into automakers in Japan, America, and Europe was also very enlightening.
★ ★ ★ ★ ★
william
This book should be read by every business student. It is a perfect summary of 20th century's industrial development.
This book also provides a perfect insight to large scale academic programs and reseachs. Every student reading this book will gain much more than taking 2 or 3 courses in an MBA program. This book has much to offer than any of the books that I have read. It makes you think and then gives the answers and at the end it presents with you issues to think further.
This book also provides a perfect insight to large scale academic programs and reseachs. Every student reading this book will gain much more than taking 2 or 3 courses in an MBA program. This book has much to offer than any of the books that I have read. It makes you think and then gives the answers and at the end it presents with you issues to think further.
★ ★ ★ ★ ★
dini
Although this book was required reading in my first days at Saturn Corporation, I still have positive memories of it being one of the more enjoyable of all my technical education reads of my engineering career. It really helps when an author can take an engineering process and bring it to life. The fact that he could describe the process by relating a supposedly non-technical event was amazing; and perhaps why it was so enjoyable. Education can be fun when approached right; and this author did that.
Now that I'm writing books, I hope I can relate to my own readers as well.
Now that I'm writing books, I hope I can relate to my own readers as well.
★ ★ ★ ★ ★
jackilynne82
A landmark study. The agony and failures of the big three Detroit automakers, compared to the continuing success of Toyota and other innovative companies like Honda, demonstrate the effectiveness of what the authors describe as Lean Production. A 'must read' to understand some of the history of how their products came to be consistently rated at the top in quality, engineering, reliability, and dependability.
★ ★ ★ ★ ★
kim lindner
I first read this books several years ago. Recent events caused me to pick it up again. The author compares Toyota with other American and European car companies. I is pretty clear why they are in trouble. The domestic car industry peaked in 1955 and has been on a roller coaster ride since then. If you also read Lee Iococca's recent book you get a clear picture of how out of touch the big three executives really are.
★ ★ ★ ★ ★
doan nguyen
"The Machine" is a foundational work which peers into the heart of Toyota's production system and verifies through metrics that the way they have done business is measurably superior to other companies, both in similar automotive industries, and outside of the auto industry. Jim Womack and his team from MIT do a superior effort and provides a very good overview of Lean production and should be included in any ernest study of Lean principles.
★ ★ ★ ☆ ☆
kristen moniz
If you are just starting out learning about Lean Manufacturing, and you only have time to read one book, "The Machine that Changed the World" is an historically important book but "Lean Thinking" is the one that actually gets you started toward implementation. It's one of those rare occasions where the sequel was better than the original.
★ ★ ★ ★ ☆
caryn winslow
Great book. I am no expert in manufacturing techniques, but I found the book readable, almost like a novel. Gives a good insight into the car industry up to 1990, and I would love to see a second edition of this, given all the changes in the 90's.
The only downside I could find is that the book gets a little repetitive at the end.
The only downside I could find is that the book gets a little repetitive at the end.
★ ★ ★ ★ ★
clover
A small group of firms in a country devastated by war rose to the top in one of the world's most competitive industries. Only by thinking of the way things were done, and why. Everyone connected to the automobile should read this book, and review how things are done in his company.
★ ★ ★ ★ ★
m r sethi
For interesting and thought provoking book. The big three, as well as American in general, is reaping that which we failed to grasp 30 years ago - the need for lean and a different approach to manufacturing overall. This book is very concise and informative with adequate data to back up its conclusions.
★ ★ ☆ ☆ ☆
katie adee
This and other books on Lean and the Toyota Production System, while valuable, present a very one-sided, idealized and incomplete view. To get the view from the inside, you must read Notes from Toyota-Land: An American Engineer in Japan. You will also learn surprising things about Japanese culture.
★ ★ ☆ ☆ ☆
daphne cheong
It is now 2011 and Hyundai's manufacturing model is showing substantial superiority to the Toyota model of "lean production."
While book makes some valid and relevant points as to why Toyota's model is superior to the conventional Detroit model of mass production, it fails to address the failures of the "lean production" system, namely the massive recalls of Toyota products. The book also makes some fairly outlandish and frankly preposterous claims of the "lean production" system becoming the dominant manufacturing system worldwide. A system that Hyundai tried implementing but failed, adapting instead, a system controlled and managed by engineers and scientists driven by information technology. In contrast to a highly trained and skilled common work force of Toyota's "lean production" model.
Hyundai's model so far has been superior to the Toyota model resulting in remarkable gains in quality, market share and a superior development time frame. In fact, LG and Samsung are also showing far more resilience and market penetration than any of their Japanese electronic counterparts.
Hyundai's model is also far more adaptable to exporting their factories, resulting in greater penetration into developing markets than Toyota's model. Hyundai has factories in China, the United States, the Czech republic, India and bringing factories online in Russia and Brazil as well. Toyota's model requires years of training or the exportation of vehicles from Japan, limiting their adaptability to the markets in which they sell.
The authors show definite favoritism in their bias for Toyota which clouds their judgment and lead them to far fetched conclusions that have, number one, not been realized and, number two, have at best, failed. Toyota's model is not revolutionizing world industry. In fact, it is failing and failing in spectacular fashion.
These same authors must have been part of the original MIT think tank in the early 1990's that concluded Hyundai essentially had no chance in competing against Japan's and Toyota's, in particular, model of "lean production." The Japanese industry felt much the same way and never really took Hyundai as a viable competitor until it was too late. It is now a matter of time until the inevitable takes place and Hyundai supplants Toyota as the best auto manufacturer with the most highly desired products in the industry. Like what Toyota did to GM and Ford, Hyundai is now poised to do to Toyota and Honda.
It will be interesting to see how Toyota adapts to the new challenge posed by Hyundai. Their "lean production" model has essentially failed and will need some serious modifications in order to make Toyota competitive once again. If history is any guide, Toyota may not recover, even with what the authors' believe is the superior manufacturing system. The Japanese ship building industry isn't competitive with the Koreans and neither is the Japanese electronics industry. In fact, in the United States, Apple is doing very much similar to what Hyundai is doing. Designing and engineering superior products and modularizing the manufacturing process. Apple is the most successful personal electronics company on the planet and vastly more successful than Sony. GM and Ford are looking like they are following the same path and are becoming competitive again also.
It isn't about labor relations either. Hyundai's relationship with it's unionized Korean workers has always been quite adversarial, even more so than GM and Ford. Yet Hyundai puts out world class products. Hyundai, however, has a very good relationship with their Alabama workers much like the Japanese do with their United States plants.
All in all, the book is an interesting read. However, the authors, somehow come to an erroneous conclusion that Toyota's system of "lean manufacturing" is superior to all others and have let that premise blind them to believe that nothing else could ever be better or supplant it. Hyundai and Apple are showing otherwise with a remarkable resilience and tremendous success using a much different model. Especially in how both were relegated to the grave by the so-called pundits, even the experts at MIT.
While book makes some valid and relevant points as to why Toyota's model is superior to the conventional Detroit model of mass production, it fails to address the failures of the "lean production" system, namely the massive recalls of Toyota products. The book also makes some fairly outlandish and frankly preposterous claims of the "lean production" system becoming the dominant manufacturing system worldwide. A system that Hyundai tried implementing but failed, adapting instead, a system controlled and managed by engineers and scientists driven by information technology. In contrast to a highly trained and skilled common work force of Toyota's "lean production" model.
Hyundai's model so far has been superior to the Toyota model resulting in remarkable gains in quality, market share and a superior development time frame. In fact, LG and Samsung are also showing far more resilience and market penetration than any of their Japanese electronic counterparts.
Hyundai's model is also far more adaptable to exporting their factories, resulting in greater penetration into developing markets than Toyota's model. Hyundai has factories in China, the United States, the Czech republic, India and bringing factories online in Russia and Brazil as well. Toyota's model requires years of training or the exportation of vehicles from Japan, limiting their adaptability to the markets in which they sell.
The authors show definite favoritism in their bias for Toyota which clouds their judgment and lead them to far fetched conclusions that have, number one, not been realized and, number two, have at best, failed. Toyota's model is not revolutionizing world industry. In fact, it is failing and failing in spectacular fashion.
These same authors must have been part of the original MIT think tank in the early 1990's that concluded Hyundai essentially had no chance in competing against Japan's and Toyota's, in particular, model of "lean production." The Japanese industry felt much the same way and never really took Hyundai as a viable competitor until it was too late. It is now a matter of time until the inevitable takes place and Hyundai supplants Toyota as the best auto manufacturer with the most highly desired products in the industry. Like what Toyota did to GM and Ford, Hyundai is now poised to do to Toyota and Honda.
It will be interesting to see how Toyota adapts to the new challenge posed by Hyundai. Their "lean production" model has essentially failed and will need some serious modifications in order to make Toyota competitive once again. If history is any guide, Toyota may not recover, even with what the authors' believe is the superior manufacturing system. The Japanese ship building industry isn't competitive with the Koreans and neither is the Japanese electronics industry. In fact, in the United States, Apple is doing very much similar to what Hyundai is doing. Designing and engineering superior products and modularizing the manufacturing process. Apple is the most successful personal electronics company on the planet and vastly more successful than Sony. GM and Ford are looking like they are following the same path and are becoming competitive again also.
It isn't about labor relations either. Hyundai's relationship with it's unionized Korean workers has always been quite adversarial, even more so than GM and Ford. Yet Hyundai puts out world class products. Hyundai, however, has a very good relationship with their Alabama workers much like the Japanese do with their United States plants.
All in all, the book is an interesting read. However, the authors, somehow come to an erroneous conclusion that Toyota's system of "lean manufacturing" is superior to all others and have let that premise blind them to believe that nothing else could ever be better or supplant it. Hyundai and Apple are showing otherwise with a remarkable resilience and tremendous success using a much different model. Especially in how both were relegated to the grave by the so-called pundits, even the experts at MIT.
★ ★ ☆ ☆ ☆
huntie
The Machine That Changed the World and the subsequent articles that Mr. Womack has written for the Wall Street Journal almost make him look like a shill for Toyota. This book either omits or minimizes the importance of developments that lead Toyota to the Toyota Production System. I expected a more independent and intellectually honest viewpoint because Mr. Womack passes himself off as a top academic.
★ ☆ ☆ ☆ ☆
reena
Here is something that will blow your mind. Go to Wikipedia and you will see that Toyota got all of its philosophy from the originator of material reduction (JIT) and efficiency from:
Piggly Wiggly grocery stores. That's right, "Piggly Wiggly"!!!!
If you don't believe me then go to this Wikipedia website- [...]
and read it for yourself. Piggly Wiggly was so successful that they dominated the grocery industry across the nation and the government had to intervene because they were making too much profit (fair and square) and the other grocers could not compete. Read how Toyota came an adopted their entire system and that TPS is really PWS "The Piggly Wiggly" system.
I have said repeatedly that all of these Lean books are crap and a bunch of junk that these people are lining their pockets with. They have done the worst research, study, and experience possible. Again, manufacturing is a science, not cooked up recipes with cookie cutter processes that fixes what ales you.
Piggly Wiggly grocery stores. That's right, "Piggly Wiggly"!!!!
If you don't believe me then go to this Wikipedia website- [...]
and read it for yourself. Piggly Wiggly was so successful that they dominated the grocery industry across the nation and the government had to intervene because they were making too much profit (fair and square) and the other grocers could not compete. Read how Toyota came an adopted their entire system and that TPS is really PWS "The Piggly Wiggly" system.
I have said repeatedly that all of these Lean books are crap and a bunch of junk that these people are lining their pockets with. They have done the worst research, study, and experience possible. Again, manufacturing is a science, not cooked up recipes with cookie cutter processes that fixes what ales you.
Please RateThe Story of Lean Production-- Toyota's Secret Weapon in the Global Car Wars That Is Now Revolutionizing World Industry